What are the characteristics of pure tungsten as an electrode?
Pure tungsten electrodes (WTEs) have several distinctive characteristics that make them suitable for specific applications, particularly in welding processes such as Tungsten Inert Gas (TIG) or Gas Tungsten Arc Welding (GTAW). Here are some key characteristics:
1. High Melting Point: Tungsten has one of the highest melting points among metals, at approximately 3,422°C (6,192°F). This property allows the electrode to maintain its structural integrity at high temperatures, making it ideal for arc welding.
2. Low Evaporation Rate: Pure tungsten has a low evaporation rate even at very high temperatures, which helps in maintaining the shape and size of the electrode during welding operations.
3. Good Electrical Conductivity: Tungsten is a good conductor of electricity, which is essential for efficient arc generation and maintenance during welding.
4. Chemical Stability: Tungsten is highly resistant to chemical reactions, especially with oxygen and other gases. This characteristic reduces the risk of contamination of the weld pool and helps maintain the purity of the weld.
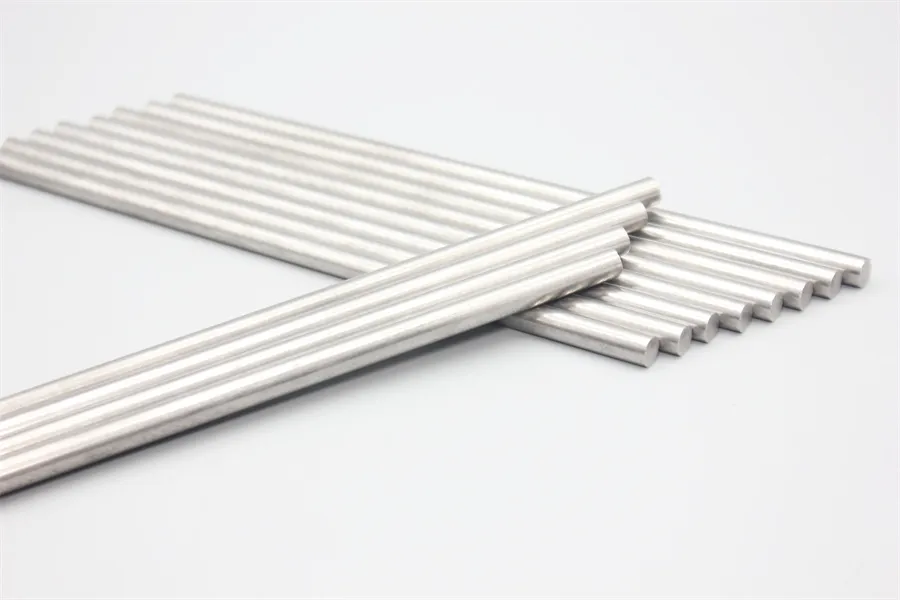
5. Low Heat Generation: Despite its high melting point, tungsten does not generate excessive heat on its own, which helps in controlling the temperature of the welding process and prevents overheating of the electrode.
6. Color and Appearance: Pure tungsten electrodes typically have a silver-gray color and a smooth surface. They are often marked with green bands to distinguish them from other types of electrodes.
7. Suitability for Specific Applications: While pure tungsten is effective, it is often mixed with small amounts of thorium, cerium, or other elements to improve its performance in certain welding scenarios. However, pure tungsten is preferred for its chemical stability and low evaporation rate in non-highly active gas environments.
Despite these advantages, pure tungsten electrodes can be more prone to contamination and require careful handling and cleaning to ensure optimal performance. They are commonly used in applications where precise control over the welding arc and minimal electrode wear are required.